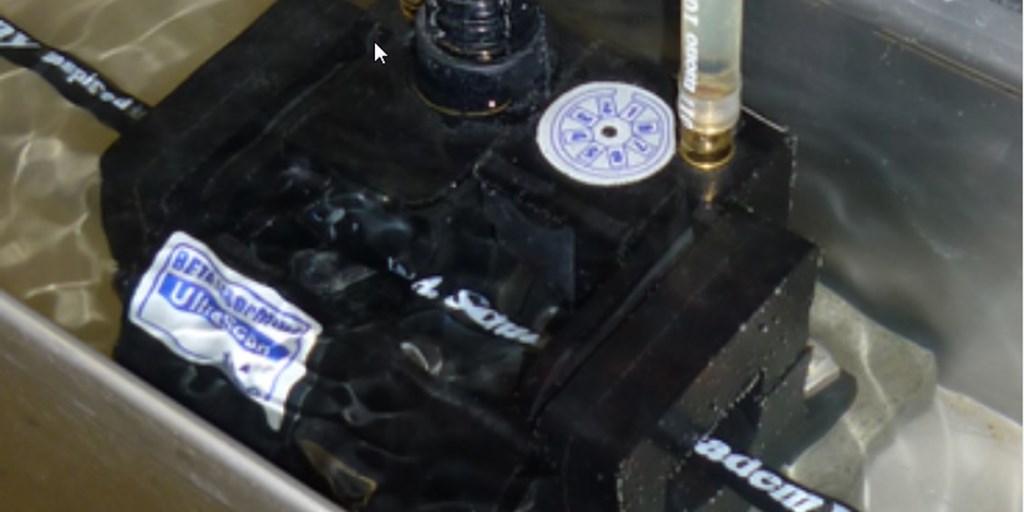
Ultrasonic wall thickness gauging offers many advantages to manufacturers of cylindrical tube-like products. In plastic pipe and tube (as well as wire and cable) manufacturing processes, non-contact measurements can be made to detect out-of-tolerance conditions with product wall thickness. Wall thickness concentricity of a formed plastic pipe or tube can be monitored on a continual and automated basis to precisely control the extrusion process without the need to shut down the manufacturing operation to manually check dimensions. Similarly, when a process requires accurate measurement of thin-walled tubing, for example, ultrasonic gauging enables you to capture thickness measurements along the total length. All in all, ultrasonic gauging is a fast, reliable and versatile method unlike manual gauging techniques.
Before we move any further, let you me give you a brief background on ultrasonic gauging.
History of Ultrasonic Gauging
The first endeavors to use ultrasonic testing to detect flaws in solid materials occurred in the 1930s. And the first commercial application was introduced in the late 1940s. By the 1970s, equipment manufacturers optimized these gauges, making them compact, more precise and versatile to meet a wide range of measurement applications. Further advances in microprocessor technology delivered new levels of performance as can be seen in the latest solutions on the marketplace today.
How Does Ultrasonic Measurement Work?
The ultrasonic wall thickness gauge consists of a fixture holding multiple ultrasonic transducers around the tube. A transducer is an electronic device that converts energy from one form to another.
The ultrasonic gauge sends an electrical drive pulse and the transducers convert that energy into an ultrasonic sound wave.
Echoes are sent back to the ultrasonic transducers from the walls of the product (such as plastic pipe or tube) and the transducers convert that energy into an electrical waveform.
Depending on the degree of coverage and accuracy requirements, the ultrasonic gauging system can use multiple transducers. Each transducer generates an ultrasonic signal that is capable of measuring one layer or multiple layers of a product. With multi-layer plastic pipe or tubes, an echo occurs at each layer and each layer can be measured individually.
What Are the Latest Measurement Advances?
The latest ultrasonic wall thickness gauging solutions include high-performance operation and productivity-enhancing features. For example, NDC’s UltraScan Pro gauge (from the BETA LaserMike product line) can measure a wide range of product sizes to tackle most wall thickness measurement applications. It’s also equipped with “Snap Technology” for the automated setup of ultrasonic waveforms, making waveform setup instantaneous and completely automatic. UltraScan Pro also includes multi-layer and thin wall thickness measurement capabilities for measuring up to 4 layers and the smallest of wall thicknesses. There’s also a high-speed tolerance checking feature to check short-term wall variations on each individual layer of the product. (The Ultrascan Pro system is capable of making 10,000 wall measurements per second. And that’s ultrafast.) In addition to wall thickness measurements, this gauge has option to measure the ovality and outer diameter of small-to-large size products.
Are You Ready for Industry 4.0?
Communication and connectivity are key aspects of gauging today. And they’re capabilities that today’s manufacturers must consider when selecting the right ultrasonic wall thickness measurement system for their production processes. When it comes to supporting Industry 4.0, be sure your ultrasonic gauging system provides comprehensive communications and supports broad Ethernet connectivity such as ModBus TCP, Ethernet/IP, Profinet IO, Profibus DP and DeviceNet. Having these capabilities lay the foundation for improved operational control and enhanced processing capabilities for efficient production performance.
Looking for Precision, Performance and Value?
The latest in ultrasonic gauging enables pipe, tube, wire and cable makers to better control product wall thickness and concentricity — and to advance their manufacturing operations. Gauging systems that integrate seamlessly into networked production environments promote better data exchange, tighten manufacturing operations, increase process efficiency, save on material costs and improve product quality.
If you’re looking for precision, performance and value, think of NDC and check out our solutions for ultrasonic wall thickness gauging.
Intelligence that transforms the world.